Andrés Bustos, elisa López, Jesús Camacho, Hector Barrios
Abstract: El objetivo de este artículo es identificar a través de mediciones con Cartas Balance el desperdicio que ocurre en los procesos de construcción, analizado en un proyecto de edificación comercial en Zapopan, México. La metodología se utilizó para medir la productividad de las cuadrillas durante jornadas completas de trabajo, donde una vez evaluado el rendimiento de producción, se identifican las mejoras que el sistema de producción puede tener. Finalizado este proceso se implementó el Last Planner System ®, sistema ampliamente reconocido en la filosofía de Lean Construction. Se comparan los resultados de productividad de un proyecto llevado con un sistema tradicional de construcción, con un sistema de mejora continua como el Last Planner System ®. Dicha implementación, permitió que se lograra aumentar la productividad un 13% y disminuir los desperdicios un 20%, evaluados mediante la planeación de propuestas de metas y juntas diarias, la evaluación de estas con porcentajes de actividades cumplidas y sus respectivas razones de incumplimiento.
Palabras clave: Lean Construction, Last Planner System ®, Productividad, Cartas Balance.
1. Introducción
En el sector de la construcción los trabajadores son, por lo general, sometidos a grandes presiones de trabajo impuestas por sus superiores debido a los tiempos de entrega que ellos manejan, como consecuencia se presentan desperdicios durante los procesos que traen como consecuencias entregas a destiempo y retrabajos que atentan directamente al costo, los cuales no siempre reflejan el valor que el cliente desea recibir. El propietario desempeña un papel importante en la verificación y el control de los planes del contratista general en términos de tiempo, costo y calidad de la construcción (Luong Le et al, 2020). Es por ello que Lean Construction ofrece una filosofía que vale la pena estudiar y analizar en este proyecto.
Para alinear los objetivos de las herramientas individuales con Lean Construction, se consideran y enumeran 12 (doce) objetivos de Lean Construction como; reducir las variabilidades en la planificación, el diseño y los procesos, mantener el flujo continuo de materiales y trabajo, mejor visualización, enfoque en el cliente, análisis y control de defectos, mejora de los procedimientos de trabajo, mejora continua, cultura de seguridad y mejora en la comunicación entre las partes interesadas (Salem et al. 2005 ; Ballard et al 2007). Aplicar Lean Construction en los proyectos ayuda a mejorar la transparencia y la comunicación, se enfoca en la buena planeación y en un control de procesos que aumenta la productividad.
Los proyectos de construcción siempre se consideran altamente inciertos y volátiles debido a la naturaleza del trabajo, ya que los proyectos se llevan a cabo en entornos diferentes que involucran a numerosos equipos especializados que trabajan juntos para lograr los objetivos de la construcción (Sinesilassie et al. 2017). El problema principal de ello llega desde la planeación, donde no se especifica de qué manera atacar las áreas de trabajo cuando estas pueden y deben ser atacadas, además del surgimiento de errores de logística con los materiales o en herramientas necesarias que deberían estar en el lugar de la obra cuando estos son necesitados. Como consecuencia el flujo se detiene y se presenta lo que comúnmente se conoce como “trabajo esperando trabajadores, y trabajadores esperando trabajo”.
Un buen programa de planeación puede lograr que los procesos se anticipen a este tipo de errores, evitando que se detenga el flujo de trabajo logrando una productividad de manera más eficiente, donde no se altera ni el costo, ni la calidad del trabajo. Para que ello sea posible se requiere capacitar a los profesionales encargados de la planeación, ejecución y control de los proyectos en las nuevas estrategias de gestión, con el fin de que se conviertan en facilitadores en la aplicación de los nuevos conceptos (Botero y Álvarez, 2003). Si se logra definir una buena planeación y esta se coordina adecuadamente, los tiempos de entrega podrían ser los esperados, y con ello, obtener mejor valor gracias a la productividad de dichos procesos.
La productividad es un concepto que describe la capacidad o el nivel de producción por unidad de trabajo o de equipos industriales. Por medio de la productividad se pone a prueba la capacidad de una estructura para desarrollar los productos y el nivel en el cual se aprovechan los recursos disponibles. Algunos de los aspectos indispensables que no deben olvidarse a la hora de montar una compañía que produzca bienes o servicios son: la calidad, la producción, la eficiencia, la innovación, la tecnología y los nuevos métodos de trabajo. La eficiencia del proceso es un indicador de cuán eficientemente se utilizan las horas de trabajo. (Goh y Miang Go, 2019)
La industria de la construcción presenta unos niveles de productividad muy bajos en comparación a otros, y éstos, usualmente son normalizados por parte de los trabajadores y los jefes. En comparación con otros fabricantes, en la industria de la construcción, incluso de los países desarrollados, se desperdicia un alto porcentaje del tiempo del proyecto, con bajas tasas de eficiencia en el trabajo, altas tasas de accidentes y altos niveles de defectos y reprocesos (Koskela, 1992). Según el McKinsey Global Institute, “el gasto relacionado con la construcción representa el 13% del PIB mundial, pero el crecimiento anual de la productividad de estos sectores sólo ha aumentado un 1% en los últimos 20 años” (MGI, 2017).
En la mayor parte de los casos, el cliente no está consciente de que gran parte de lo que él está pagando no le está generando valor, por lo que es necesario hacer ajustes y/o aumentos que logren beneficiar tanto al cliente, como al contratista y a la mano de obra. Un aumento significa que se puede proporcionar un mayor valor a los clientes con los mismos recursos o menos, lo que se traduce en una combinación deseable de estructuras de mayor calidad a un costo menor para los propietarios, una mayor rentabilidad para los contratistas y salarios más altos para los trabajadores. Solo las transformaciones agregan valor al cliente. Por lo tanto, los flujos deben estudiarse muy bien para eliminar los desperdicios en el proceso de producción, mientras que la eficiencia debería ser mayor para las transformaciones (Albalkhy y Sweis, 2019).
Es bien sabido que en la construcción existen numerosas cantidades de desperdicios las cuales no siempre son identificadas. Existen datos de estudios realizados en Chile (Alarcón, 1999) y Colombia (Botero y Álvarez, 2003), que demuestran como la jornada laboral de la construcción casi nunca es aprovechada a un 100% y todo ello afecta al proyecto en costo y tiempo la mayoría de las veces. El departamento de Ingeniería Civil y Gestión de la Construcción de la Pontificia Universidad Católica de Chile (Alarcón, 1999), realizó mediciones durante 5 años en más de 40 proyectos de construcción demostrando que la identificación de pérdidas es una herramienta efectiva para generar el mejoramiento en la construcción, donde concluyeron que el 53% del tiempo laborado es dedicado a actividades no productivas (Botero y Álvarez, 2003).
Botero y Álvarez, 2003; explican que, una vez identificadas las pérdidas, la causa de mayor frecuencia de ocurrencia de las mismas (49%), se genera por esperas en el proceso constructivo, lo cual alerta a constructores sobre la necesidad de una mejor planificación para la disposición y localización de recursos, utilización y disposición de cuadrillas de trabajo, entre otras.
El trabajo se va a enfocar en estudiar los procesos de construcción en la obra civil de una plaza comercial para evaluar detenidamente a las cuadrillas mediante mediciones con ayuda de formatos de Cartas Balance, y se va a aplicar un sistema de control en la producción que sea capaz de identificar los desperdicios que ocurren en ello de manera cuantificable. Se va a aportar con evidencia y datos estadísticos, una mejora en la productividad que beneficie al cliente y a los contratistas con un sistema de control propuesto por Last Planner System ® basado en la comunicación, la transparencia y el trabajo en equipo. Se espera poder disminuir las pérdidas que se identifiquen con el fin de plantear propuestas de mejora en las áreas que requieran innovar continuamente los procesos.
2. Métodos y metodología
2.1 Caso de estudio
Para realizar este trabajo se enfocó en analizar el caso de la obra Distrito la Perla ubicada en el municipio de Zapopan Jalisco, la cual consiste en una plaza comercial de alrededor de 18,000 m2 destinados a la moda, la tecnología y el gourmet; contando con un total de 280 locales comerciales. Se espera que la obra finalice a finales del año 2020. Ahí se evaluó y se midió a diferentes cuadrillas que realizaron trabajos de mampostería con la ayuda de Cartas Balance, y después se aplicó Last Planner System ® que pretendía mejorar la productividad en los procesos, comparando el sistema tradicional de construcción con el de Lean Construction.
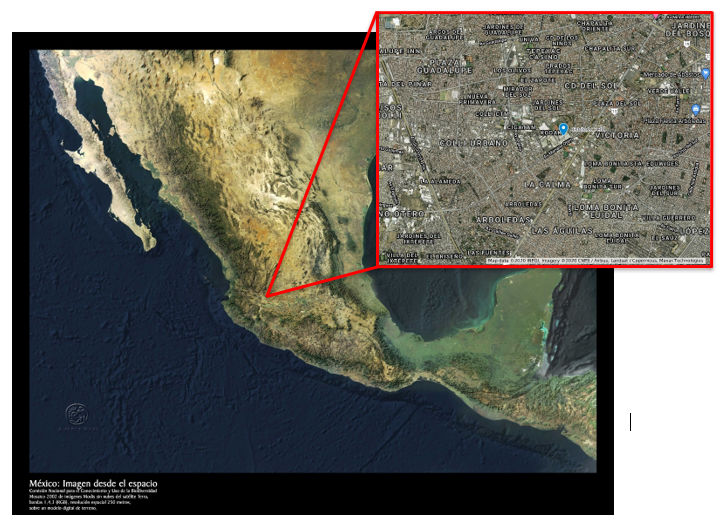
2.2 Cartas Balance
Para comenzar con el análisis del proyecto fue necesario realizar una serie de mediciones base durante tres semanas acerca de la productividad que existía en las áreas de trabajo con el método tradicional. Para ello se utilizaron formatos de Cartas Balance que nos permitían obtener de forma porcentual respecto a una jornada laboral, cuanta productividad se aportaba y canto desperdicio se conseguía. Estos resultados serían comparados con una segunda y posterior medición, realizada una vez que se implementaran mejoras de Last Planner System ®.
Una Carta Balance es una herramienta que ayuda a describir de forma detallada el proceso de una actividad mediante datos estadísticos con el fin de buscar su optimización identificando las acciones que producen valor, las que contribuyen a generarlo, y sus pérdidas. Para ello existen formatos donde se registra en cada intervalo de tiempo la actividad realizada por el obrero. (Pérez et al, 2019)
Para poder realizar mediciones con Cartas Balance se necesita tener un espacio visual de toda la cuadrilla e identificar a los trabajadores para cuantificar su nivel de productividad. Se pueden apoyar con formatos de Cartas Balance, lápiz, cronómetro y cámaras de video. Los datos deben tomarse en intervalos de un minuto, máximo dos, durante jornadas de 3 y 4 horas para lograr que las mediciones tengan validez confiable.
En el formato deben estar identificadas las actividades como:
Trabajo productivo (TP): Es aquel trabajo que produce valor de forma directa y refleja lo que el cliente desea.
Trabajo contributorio (TC): Es el proceso que no genera valor, sin embargo, aporta de manera indirecta para generar el producto para el cliente.
Trabajo no contributorio (TNC): Es la actividad que no genera valor ni aporta al avance del proyecto, (conocidas también como pérdidas o tiempos muertos).
Además, el formato debe especificar qué actividades fueron cada una de ellas de las que generan valor, las que contribuyeron a generar valor y las que no generan valor. Se recomienda usar abreviaturas en las mediciones. Para mayor detalle sobre los ejemplos más comunes utilizados en las Cartas Balance, ver Tabla 1.
Tabla 1. Ejemplos de Trabajo Productivo, Trabajo Contributorio y Trabajo No Contributorio de Cartas Balance
Trabajo Productivo (TP) | Trabajo Contributorio (TC) | Trabajo No Contributorio (TNC) |
Vaciar concreto | Medir | Esperas |
Levantar muro | Instrucciones | Retrabajos |
Habilitar acero | Reubicación de material | Ausencia |
Detallar muro | Búsqueda de material | Tiempo Ocioso |
Pintar | Orden y limpieza | Viajes |
Colocar instalación | Transporte | Descansos |
Los datos que se toman en campo deben ser cuantificados en una hoja de cálculo que permita desglosar y visualizar los resultados de manera gráfica y porcentual para lograr detectar cuánto valor se está generando del total de una jornada y como mejorar ese porcentaje sin perder la calidad, ni alterar el costo. (Produktiva, 2018)
Para el caso de estudio, se tomaron mediciones en intervalos de dos minutos durante aproximadamente 18 jornadas de trabajo desde 4 hasta 7 horas. En cada una de las Cartas Balance se realizaban anotaciones, comentarios, pérdidas identificadas y gráficas que mostraran de forma visual los porcentajes de productividad durante la jornada del día (ver Figura 2).
Esta técnica presenta múltiples ventajas por su sencillez ya que tiene validación estadística, permite medir la variabilidad de las diferentes actividades durante la obra y permite detectar oportunidades de mejora en los proyectos de construcción, situación no evidente utilizando los sistemas tradicionales de control de la producción.
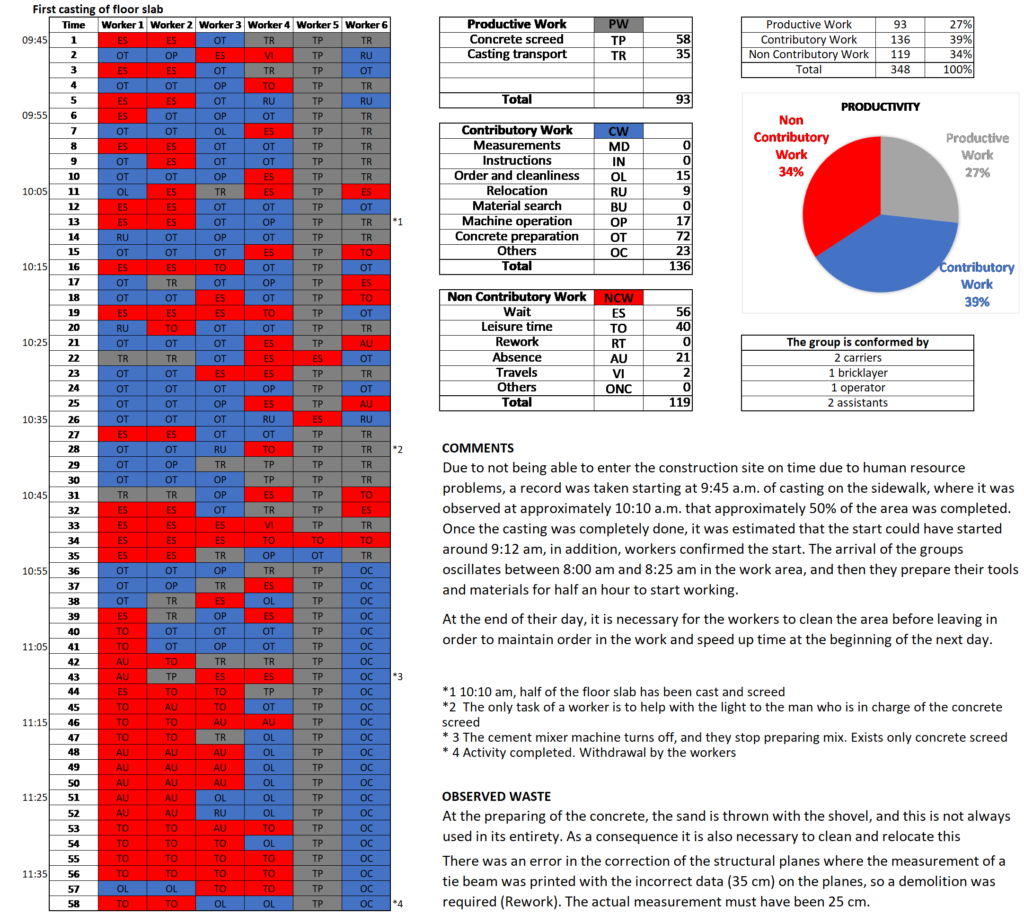
Después de obtener resultados cuantificados e identificados a detalle las pérdidas y los tiempos muertos por parte de la cuadrilla, se podrá proponer soluciones de mejora para lograr facilitar los procesos que generan trabajos productivos y disminuir las pérdidas. Para tomar una decisión es necesario que esta logre generar un impacto en el aumento de la productividad de la cuadrilla y flujo del proyecto. Se debe entender que en algunos casos la medida correctiva podrá resultar insignificante en algunos casos, o con soluciones costosas en otros, pero siempre evitando que dicho costo sobrepase lo generado por la obra.
En la Figura 3 se muestra una gráfica de base que sirvió de partida para el arranque de la implementación de Last Planner System ® donde se observa como el trabajo no contributorio está por encima del trabajo productivo y servirá de comparación de resultados finales.
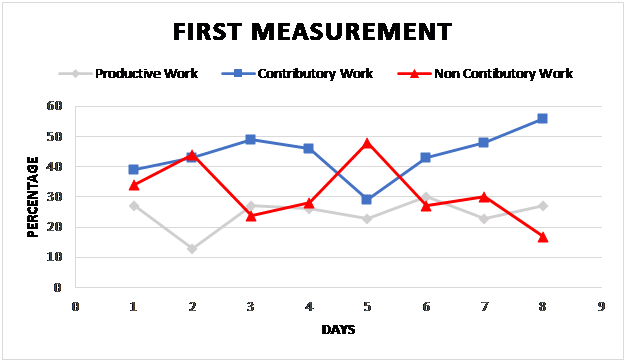
2.3 Implementación de Last Planner System ®
Last Planner System ® (El último planificador) se define como “un sistema de control de producción necesario en los proyectos para apoyar el trabajo hacia los logros planificados, realizar lo que se puede hacer para avanzar en un camino planeado y, cuando eso sea imposible, determinar caminos alternativos que cumplan con los objetivos deseados.” (Hoyos, 2018).
Su principal meta es atacar las áreas de desperdicio en la construcción que implican [trabajadores esperando trabajo y trabajo esperando trabajadores], además de tomar el control del proyecto y la toma de decisiones en el tiempo adecuado. Dicho sistema de control debe ser transparente con los trabajadores y con el cliente el cual pueda generar un círculo de confianza con todos los involucrados. Last Planner System ® puede superar la variabilidad dentro de la construcción al considerar la planificación y la colaboración como los elementos clave para lograr los objetivos de Lean Construction. (Ballard, 1993). Lean Construction considera la construcción como una unidad de producción que tiene que pasar por ciertas fases desde el inicio del proyecto hasta el cierre del proyecto (Aslam et al, 2020).
Existen muchas maneras de realizar Last Planner System ®.
- Identificar los trabajos productivos, trabajos contributorios y trabajos no contributorios.
- Pull Planning
- Porcentaje de actividades cumplidas y razones de incumplimiento
- Reducir la variación y mejorar el flujo de trabajo
- Trabajo en equipo y comunicación
- No trabajar bajo supuestos
Los principales puntos utilizados en este proyecto fueron la identificación de trabajos productivos, contributorios y no contributorios con ayuda de los formatos de Cartas Balance. El “Pull Planning” basado en la propuesta de objetivos y metas la realización de juntas diarias y semanales, y para llevar un control de ello, realizar los porcentajes de actividades cumplidas y las razones de incumplimiento.
2.3.1 Pull Planning
El primer proceso a utilizar para el proyecto fue Pull Planning. Según Tsao et al. 2014, “Es un proceso de planificación colaborativa donde los ejecutantes del proyecto trabajan juntos para diseñar el proceso para lograr un hito. El término ‘Pull Planning’ se refiere al concepto lean de ‘pull’ como una solicitud desde abajo en lugar del ‘push’ de arriba hacia abajo como se aplica en la práctica tradicional” (planear desde el final, hacia el comienzo).
Para este proceso, primero se realizó un inventario de trabajos pendientes con sus respectivas restricciones con el fin de poder identificar las metas a realizar, y brindar apoyo hacia la mano de obra para facilitarles el trabajo escuchando sus peticiones, sus avances y sus comentarios, este fue el primer paso para lograr una mayor comunicación con ellos. A continuación, se anexa el inventario en Tabla 2:
Tabla 2. Inventario de trabajos pendientes.
El subcontratista ha realizado albañilerías en numerosas ocasiones en la obra de Distrito la Perla, entre ellas se encuentran colados de dalas y banquetas, además de levantamientos de muros. Actualmente se encuentran en la elaboración de cuatro montacargas en la misma zona con diferentes cuadrillas por nivel (sótano 2, sótano 1, planta baja y planta alta). |
Montacargas Sótano 2 | Cuadrilla de tres personas. Es la obra menos avanzada de todas. Solo hay avance del colado de la dala inferior, el ritmo de trabajo es lento, no hay material para descimbrar, ni block para levantar muro. No se había solicitado el material para que la cuadrilla pudiera avanzar. |
Montacargas Sótano 1 | No se sabe el tamaño de la cuadrilla. Solo se observaron dos personas trabajando. Obra parcialmente avanzada, pero con retrasos. Fue la obra que se inició primero, y no se ha terminado. Los muros principales ya se encuentran casi levantados, falta cimbrar para colar dalas y castillos y poder continuar los muros de los lados, falta terminar de cimbrar una dala principal de la que dependerá el avance de la obra. Se observa como cuando terminan de levantar muro, colocan armado y no se realiza el colado ni la cimbra, se sigue levantando muro por otro lado hasta llegar al nivel de dala. Faltan detalles de muros, limpieza del área, y traer más material. |
Montacargas Planta Baja | Cuadrilla de 5 personas. La cuadrilla está incompleta, no existe información sobre la ausencia de los trabajadores. Falta levantar tres muros, colar castillos y dalas (algunas cimbras ya se encuentran colocadas, otras no), no se han detallado muros ni limpiado las partes ya terminadas. Existe un exceso de inventario (armados de acero elaborados sin colocar debido a la lentitud del levantamiento de muro) no hay limpieza del área. |
Montacargas Planta Alta | Cuadrilla de 6 personas. Obra avanzada. Falta colar dalas, levantar el resto de los muros, detallar los muros ya levantados, colar dalas y castillos. Existe mayor organización y limpieza que en otras obras observadas. Se realizan detalles de forma parcial sobre los muros levantados. El material comienza a agotarse (block, arena y grava). |
Con ayuda del inventario (Rojas, 2016) y con algunos residentes de la obra, se organizó una junta donde se plantearía la propuesta de metas diarias para cada cuadrilla. En ella se especifica la meta semanal, y el desglose de actividades que se tienen que llevar a cabo, día a día, desde el final hacia el comienzo (de adelante hacia atrás). Dichas metas fueron presentadas a cada una de las cuadrillas preguntándoles si para ellos era posible realizar las actividades que se proponían para llegar a ello, y que necesitaban de los superiores para ayudarles a hacer su trabajo.
Para evitar errores y re-indicaciones con las actividades que se propusieron, dichas metas y actividades se mantenían colocadas en obra sobre un tablero elaborado de forma manual (Figura 4) con notas de colores donde se dividía por:
- Actividades Semanales (notas naranjas)
- Actividades Diarias (notas azules)
- Pendientes que faltan (notas rosas)
La última sección se encargaba de colocarle a los residentes alguna herramienta, material o revisión que los trabajadores requerían para poder seguir laborando y no detenerse.
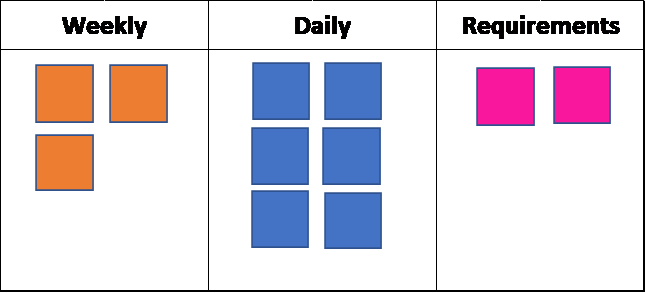
A partir de ello, se plantearon juntas diarias con los trabajadores en la mañana donde se dialogaba cuantas de las actividades propuestas si se cumplieron y cuáles no, además de los motivos del por qué no pudieron llevarse a cabo. Los cambios y modificaciones que se realizaban sobre la marcha también fueron anotados y a partir de ello se llevaba registro diario de las actividades propuestas sobre las actividades realizadas. Con esos datos, se realizaban además juntas semanales con los superiores para revisar y plantear cómo mejorar las actividades día a día procurando cumplir el 100% de las metas. Esto se llevó a cabo por varias semanas donde cada día se llevaba registro (ver Tabla 3) y se proponían soluciones semanales.
Tabla 3. Fragmento de tabla del día 17 de febrero con metas propuestas, metas modificadas y actividades realizadas.
Date | Area | Proposed goals | Modified goals | Performed activities |
Feb 17 | Basement 1 | • Raise the wall up to the 2nd concrete tie beam axis G (13-14) and H (13-14). • Enable steel for the second concrete tie beam 45 cm length of axis G (13-14) and H (13-14). | • Casting of first concrete tie beam with embedded plate axis H (13-14) • Raise wall to second plate, in concrete tie beam, G axis (13-14) • Enable steel for second concrete tie beam G axis (13-14) • Raise wall up to third concrete tie beam with G axis plate (13-14) • Raise wall to second concrete tie beam with H axis plate (13-14) • Enable 1st steel concrete for tie beam in axle 13 pocket (G-H) | • Casting of first concrete tie beam with embedded plate axis H (13-14) • Enable 1st steel concrete tie beam in axle 13 pocket (G-H) |
Feb 17 | Ground Level | • Remove formwork from 1st concrete tie beam • Build wall until second concrete tie beam G (13-14) and H (13-14) axes, ladder • Correct overlaps in left concrete wall stud H-axis forklift door (13-14) • Enable steel for 35 cm closing wall in H-axis forklift door (13-14) | • Raise 4 rows of block in G-H axis (13-14) • Enable steel, formwork and casting for the first concrete tie beam in pin axis 14 (G-H) • Demolish a row of block in wall G (13-14) • Enable steel, formwork and casting for the first 40-cm length on walls with axes G (13-14) and H (13-14) | • Raise 4 rows of block in G-H axis (13-14) • Enable steel, formwork and casting for the first concrete tie beam in pin axis 14 (G-H) • Demolish row of block in wall G (13-14) |
Feb 17 | Level 2 | • Remove formwork from 2nd concrete tie beam • Build wall up to 3rd concrete tie beam • Enable steel, place formwork and cast 3rd concrete tie beam | • Enable steel, formwork and cast 3rd 30 cm length on axes 14 (G-H) and G -H (13-14) • Remove the formwork of the 3rd concrete tie beam of 30 cm G axis (13-14) • Remove concrete wall stud formwork of 20 cm axis G (13) • Remove 68 cm left concrete wall stud formwork on H-axis forklift door (13-14) • Detail keypads in 68 cm concrete wall stud on the H-axis forklift door (13-14) • Enable steel, formwork and cast concrete tie beam of closing of 35 cm in door of forklift axis H (13-14) | Enable steel, formwork and cast for 3rd 30 cm length on axes 14 (G-H) and G -H (13-14) • Remove the formwork of the 3rd concrete tie beam of 30 cm G axis (13-14) • Remove concrete wall stud formwork of 20 cm axis G (13) • Remove 68 cm left concrete wall stud formwork on H-axis forklift door (13-14) • Detail keypads in 68 cm concrete wall stud on the H-axis forklift door (13-14) • Enable steel, formwork and concrete wall stud for 35 cm closing on H-axis forklift doors (13-14) |
2.3.2 Porcentaje de Actividades Cumplidas (PPC) Al tener los datos de manera escrita, se registraron en una hoja de cálculo de manera cuantitativa para conocer de manera porcentual qué actividades estaban siendo realizadas en su totalidad con respecto al total de actividades propuestas en el día (ver Tabla 4), además se añadieron gráficas para tener una mejor visualización y poder comparar los datos semana tras semana (propuesto por Botero y Álvarez, 2005). La importancia del Porcentaje de Actividades Cumplidas (PPC) no es buscar culpables, ni señalar a los trabajadores, sino identificar por qué ocurren desperdicios en el proceso. Este proceso se realizó cada mañana antes de la llegada de los trabajadores para tener mayores posibilidades de reaccionar a qué tan cerca se avanza con respecto al plan de trabajo programado. A cada cuadrilla se le asignó su tablero con actividades diarias y, con base a él, se fue revisando cuantas actividades se realizaron, obteniendo así los porcentajes.
Tabla 4. Porcentaje de Actividades Cumplidas de cada semana, evaluando cada día a la cuadrilla correspondiente, con su porcentaje individual y total diario.
PPC Week 1 | |||||
Feb 17 | Feb 18 | Feb 19 | Feb 20 | Feb 21 | |
Basement 1 | 33% | 40% | 57% | 100% | 67% |
Ground Floor | 50% | 100% | 71% | 100% | 80% |
Level 2 | 100% | 71% | 67% | 100% | 100% |
Total | 61% | 70% | 65% | 100% | 82% |
Average | 76% | ||||
PPC Week 2 | |||||
Feb 24 | Feb 25 | Feb 26 | Feb 27 | Feb 28 | |
Basement 1 | 75% | 80% | 100% | – | – |
Ground Floor | 71% | 67% | 80% | 100% | 67% |
Level 1 | 100% | 83% | 67% | 100% | 80% |
Level 2 | 100% | 80% | – | 100% | – |
Total | 87% | 78% | 82% | 100% | 73% |
Average | 84% | ||||
PPC Week 3 | |||||
Mar 2 | Mar 3 | Mar 4 | Mar 5 | Mar 6 | |
Basement 3 | – | – | 100% | 0% | 100% |
Basement 2 | 33% | 100% | 100% | 100% | 60% |
Basement 1 | – | 100% | 50% | 100% | 0% |
Ground Floor | 80% | 50% | 75% | 100% | 40% |
Level 1 | 67% | 100% | – | – | – |
Level 2 | 100% | 100% | 100% | 100% | – |
Total | 70% | 90% | 85% | 80% | 50% |
Average | 77% | ||||
PPC Week 4 | |||||
Mar 9 | Mar 10 | Mar 11 | Mar 12 | Mar 13 | |
Basement 3 | 60% | 67% | 80% | 80% | 67% |
Basement 2 | – | 100% | 50% | 50% | 0% |
Basement 1 | 25% | 67% | 67% | 40% | 80% |
Ground Floor | 80% | 67% | 50% | 50% | 100% |
Rooftop | – | – | 100% | 100% | 0% |
Level 2 | 100% | – | – | – | 58% |
Total | 66% | 75% | 69% | 64% | 58% |
Average | 68% |
2.3.3 Razones de Incumplimiento y 5 Whys
En cada junta existió variación de actividades cumplidas cada día, y con ellas, hubo un gran número de razones de incumplimiento las cuales también se registraban de forma individual y de forma colectiva cada día.
Para la obtención de las razones de incumplimiento, se puede aplicar la teoría de los “5 Whys” (5 por qué) para encontrar la raíz del problema. La teoría es muy simple y su propio nombre lo indica, preguntar el por qué no se cumplió una actividad y sobre cada razón preguntar nuevamente el por qué en cinco ocasiones hasta encontrar un motivo que se pueda solucionar de manera colaborativa (en algunas ocasiones el problema aparece antes del quinto por qué).
Al poder identificar la raíz de los problemas, se registraron en una tabla de conteo (Tabla 5) para poder observar la frecuencia de dichas razones, cada día. Uno debe adherirse a las ideas lean fundamentales y reconocer los impulsores principales.
Con los datos obtenidos se proponían soluciones a los problemas enfrentados y se buscaba la manera de anticiparse a dichos errores con el fin de evitar que volvieran suceder. En algunos casos fue posible corregir los problemas, sin embargo, en otros, los motivos eran razones que se encontraban fuera del alcance de los residentes y superiores.
Tabla 5. Tabla de razones de incumplimiento desglosadas por cuadrillas y su frecuencia.
Causes for noncompletion (CNC) | ||||
Group 1 | Group 2 | Group 3 | Total | |
Wait for material | 4 | 1 | 5 | 10 |
Lack of tool | 2 | – | – | 2 |
Indications not followed | 1 | 1 | – | 2 |
Lack of communication | 2 | – | – | 2 |
Reworks and errors | – | 4 | – | 4 |
Time or absences | 2 | 5 | 2 | 9 |
Unforeseen changes | 3 | 3 | 3 | 9 |
Problems between workers | 3 | 2 | – | 5 |
External reasons | 2 | 2 | 4 | 8 |
B1 | GF | L1 and L2 | 51 |
La última etapa en el proceso de ejecución Lean es descubrir los arreglos de mejora y probarlos. Una vez que se prueban, deben ser actualizados. La preparación y el seguimiento son importantes en cada uno de los pasos aclarados previamente. Se debe mostrar moderación alegando que el procedimiento de uso puede llevar bastante tiempo (P. Sivaraman et al, 2020).
3. Análisis y Resultados
Desde que se inició con primera etapa de mediciones con Cartas Balance se obtuvieron porcentajes de productividad que oscilaban entre un 13% y un 27% mientras que los desperdicios oscilaban entre un 30% y un 48%. En la segunda etapa después de varias semanas implementando Last Planner System ®, se obtuvo una disminución muy notoria en los tiempos muertos presentando unos porcentajes de 20% a 24% en pérdidas y un aumento de productividad con resultados desde 25% hasta 38% (ver Figura 5).
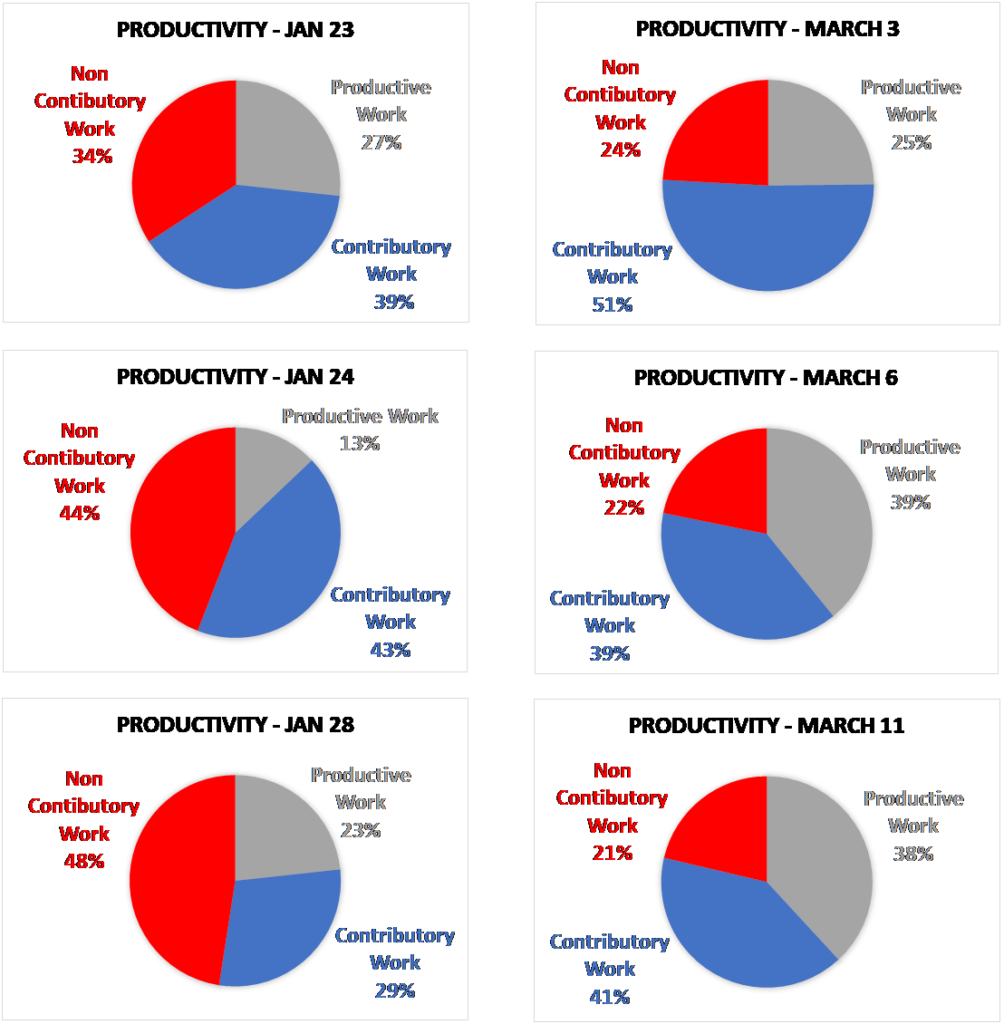
En la Figura 6 se puede apreciar el promedio de productividad en cada área de medición donde se observa el aumento de productividad desde un 21% hasta un 34% y la disminución de un 42% a un 22% en desperdicios. En la gráfica comparativa (Figura 6) se observa como en la primera medición el trabajo no contributorio estaba por encima del trabajo productivo, cuando en la segunda medición, después de implementar Last Planner System ®, obtuvimos que la productividad estuviera arriba de los desperdicios, evidenciando así la disminución de los tiempos muertos.
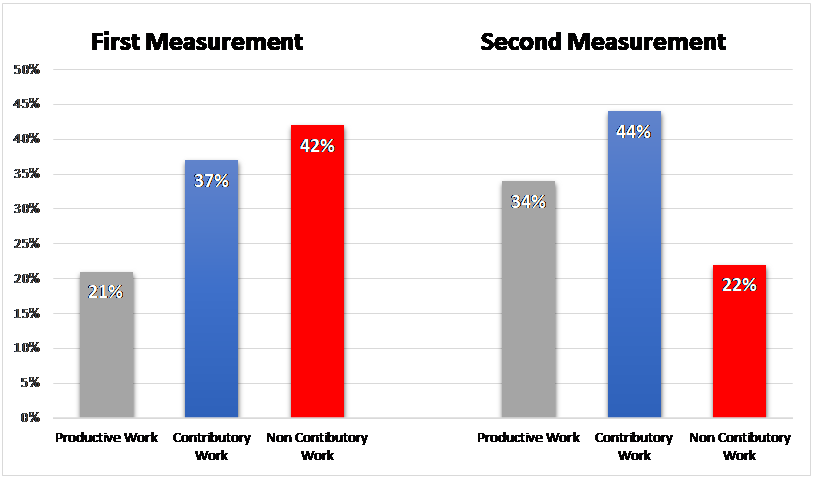
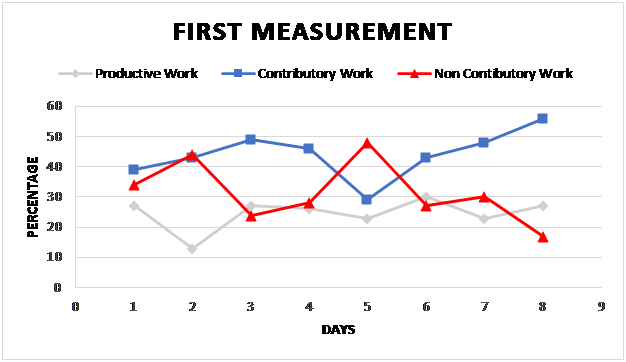
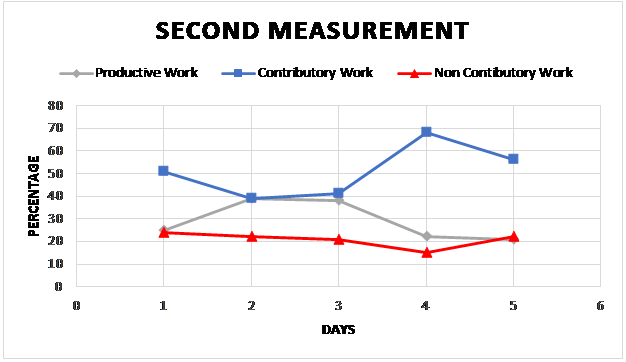
Al registrar las actividades realizadas y las no realizadas se notó mucha variación en las actividades, y no se pudo conseguir una constante ya que las razones de incumplimiento variaban cada día (Figura 8).
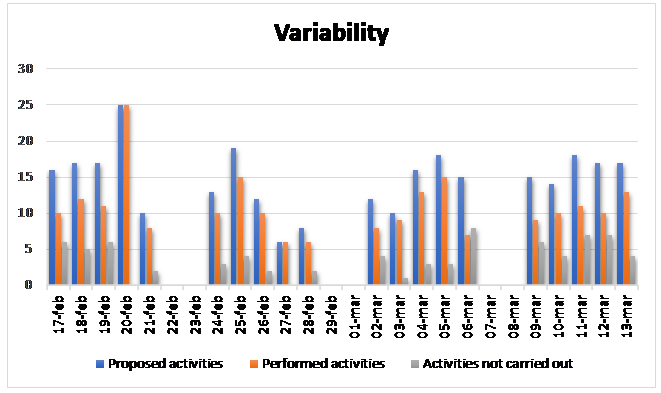
Las razones de incumplimiento más repetitivas fueron falta de material, cambios imprevistos, tiempo y faltas, y razones externas abarcando el 70% de las razones de incumplimiento (ver figura 9 para mayor detalle). Las minorías de las razones que equivalen a un 20% se componen de falta de herramienta, indicaciones no seguidas, falta de comunicación, retrabajos y errores. Recurrentemente el 10% de las razones presentadas a lo largo del análisis fueron problemas entre los obreros, donde por cuestiones de destajo decidieron trabajar por separado sin reportarlo.
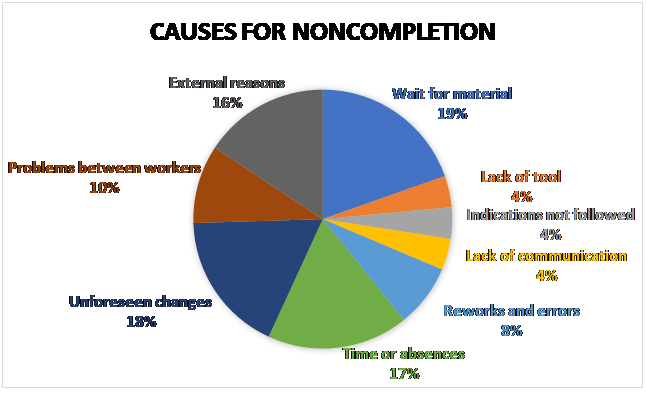
Los motivos de las razones de incumplimiento surgen desde la logística de los materiales de construcción donde su transporte hace complicada la tarea de subir material a niveles muy altos sin el apoyo de maquinaria. Al compartir la obra civil con otros subcontratistas, es muy común que se realicen cambios y acciones que puedan alterar el espacio de trabajo de otros trabajadores, como son el bloqueo o restricción del paso de personal o transporte, el mantenimiento de las áreas, instalaciones de servicios o cambios del cliente en el momento, lo que tiene como consecuencia dejar de trabajar temporalmente en esas áreas. Los cambios imprevistos de parte del contratista general también fueron muy recurrentes debido a la falta de comunicación del contratista con el jefe de los residentes quienes no recibían las indicaciones a tiempo.
4. Conclusiones
Durante el desarrollo de este proyecto e investigación sobre la construcción de una plaza comercial, en la ciudad de Guadalajara, se estudiaron los procesos de construcción por parte de la mano de obra y las indicaciones que los superiores asignan a sus trabajadores. Se pudo observar cómo presentaban numerosos detalles que debían ser corregidos y procesos que necesitan ser mejorados.
Como conclusión de ambas mediciones, se puede observar que el “trabajo no contributivo” si logró disminuir de manera significativa un 20% con las propuestas de mejoras que se implementaron con Last Planner System ®, y logró aumentar el trabajo productivo un 13%. Todavía se necesita buscar la manera de reducir el trabajo contributivo y aumentar aún más la productividad evitando el aumento de los desperdicios, mejorando continuamente los procesos (ver figura 8 para más detalle). El esfuerzo de mejora continua debe ser una respuesta natural al contexto siempre cambiante de un programa de construcción de ingeniería y gestión de proyectos (Pasquire, 2012). Estos resultados mostraron mejoras, sin embargo, pudieron ser más sobresalientes si los jefes tuvieran un acercamiento mayor con los trabajadores y con su servidor.
Dentro de los principales retos enfrentados durante esta investigación, fue la resistencia por parte de los trabajadores y la falta de compromiso por parte de los superiores quienes no mostraban interés por capacitar y motivar a sus trabajadores, además de normalizar los desperdicios y mantenerse ausentes. Al no ser una obra propia de la empresa con la que se laboró, fue difícil lograr que una persona llevara un control de varias cuadrillas cuando algunos trabajadores mostraban resistencia, y cuando los contratistas a cargo de la obra se mantenían ausentes y sin formas de comunicación.
Se demuestra que la comunicación y el acercamiento con los trabajadores genera la confianza necesaria para buscar una mayor productividad, y el no trabajar bajo supuestos genera mayor valor para el cliente. El poder identificar los desperdicios en los procesos y su raíz de problemas demuestra la capacidad para mejorar y anteponerse a dichos errores, y así, progresivamente, mejorando continuamente con el equipo de trabajo, desde los obreros, hasta los contratistas y el cliente.
Para el sistema de Last Planner System ®, su finalidad fue reducir la variabilidad mediante el trabajo en equipo, la comunicación, el porcentaje de actividades cumplidas, y la transparencia con los trabajadores y los jefes. Sus resultados fueron cuantificables y atacados en el momento para mejorar la productividad la cual gracias a el compromiso y la comunicación lograron disminuir de manera significativa en las próximas semanas mostrando mejoras en la productividad y disminución en los desperdicios.
Como aprendizaje de este proyecto se observa que los desperdicios encontrados de forma común en los procesos de construcción son consecuencia de una planeación poco eficiente por parte de los dueños cuando no apoyan del todo a sus trabajadores, y sólo exigen resultados a sus residentes sin apoyar los detalles que ellos en obra necesitan para poder sacar el trabajo que los dueños demandan. Las juntas de planeación en las mañanas, muestran mejores resultados porque existe un acercamiento y una comunicación específica que no trabaja bajo supuestos, además de comprender que la última persona que puede planificar y diseñar sus propios avances, son los mismos maestros oficiales, quienes conocen su propio rendimiento, sus tiempos, y saben cómo organizarse entre sus ayudantes. Hacer una planeación ‘Pull’ con los maestros oficiales, logrará una reducción en la variación de actividades, obteniendo un mejor cumplimiento en los procesos y mejorando el flujo de trabajo con una mejor productividad.
Es posible aplicar Lean Construction y Last Planner System ® a obras de diferente tipo siempre y cuando se apliquen los sistemas de control y se capacite al personal con la filosofía y los conceptos que se proponen. Explotar al máximo las herramientas de Last Planner System ® brinda mejores resultados y un control de producción más efectivo, además, si se aplican técnicas como Takt Planning en la programación de obra se obtiene un ritmo de trabajo que identifica las áreas que necesitan ser ejecutadas, y con ello se obtienen mejores tiempos de entregas para el cliente.
Referencias
Alarcón, L, Campero M. (1999). Administración de proyectos civiles. Santiago de Chile: Ediciones Universidad Católica de Chile. 322 p.
Albalkhy, W. & Sweis, R. (2019): Assessing lean construction conformance amongst the second-grade Jordanian construction contractors, International Journal of Construction Management, DOI: 10.1080/15623599.2019.1661571
Aslam, M., Gao, Z., & Smith, G. (2020): Framework for selection of lean construction tools based on lean objectives and functionalities, International Journal of Construction Management, DOI: 10.1080/15623599.2020.1729933
Ballard, G., Tommelein, I., Koskela, L., Howell, G. (2007). Lean construction tools and techniques. In: Best R, De Valence G, editors. Design and construction; London, UK: Routledge, Taylor and Francis Group; pp. 251–279.
Ballard, G. (1993). Lean Construction and EPC performance improvement. In: Alarcon L, editor. Lean construction. Rotterdam, The Netherlands: AA Balkema and Taylor and Francis; pp. 79–91.
Besser Lean (2019). ¿Qué es Last Planner System? [En Línea]. Recuperado de: https://besserlean.mx/last-planner-system/
Botero, L. F., Álvarez, M. E. (2003). Identificación de Pérdidas en el Proceso Productivo de la Construcción. Universidad EAFIT, Vol. 1, n.° 30, pp. 65-78.
Botero, L. F., Álvarez, M. E. (2005). Last planner, un avance en la planificación y control de proyectos de construcción Estudio del caso de la ciudad de Medellín. Ingeniería y Desarrollo, Vol. 1, n.° 17, pp. 149-159.
Comisión Nacional para el Conocimiento y Uso de la Biodiversidad (2003). México: Imagen desde el espacio. CONABIO, México. Mosaico 2002 de imágenes Modis sin nubes del satélite Terra, bandas 1,4,3 (RGB), resolución espacial 250 metros, sobre un modelo digital de terreno. [En Linea]. Recuperado de http://www.conabio.gob.mx/informacion/geo_espanol/doctos/imagenalta_febrero2003.html
Definición.de (2020). Definición de Productividad. [En Línea]. Recuperado de: https://definicion.de/productividad/
Goh, M., y Goh, Y. M. (2019). Lean production theory-based simulation of modular construction processes. Automation in Construction. Vol. 101 pp, n.° 1, pp. 227-244.
Herrera, R., y Reyes, C. (2017). Los pros y contra al implementar el sistema Last Planner en un proyecto de edificación: un caso de estudio. Ingenium, Vol. 18. n.° 35, pp. 91-104.
Hoyos, M. F., Botero, L. F. (2018). Evolución e impacto mundial del Last Planner System: una revisión de la literatura. Ingeniería y Desarrollo, Vol. 36, n.° 1, pp. 188-214.
K+K Group. (2019). ¿Cómo hacer el análisis de una carta balance? Todo lo que necesitas saber. [En Línea]. Recuperado de: https://kykconsulting.pe/como-hacer-analisis-carta-balance/
Koskela, L. (1992). Application of the new production philosophy to construction. Vol. 72. Stanford (CA): Stanford University.
Luong Le, P., Elmughrabi, W., Dao, T. M., & Chaabane, A. (2020) Present focuses and future directions of decision-making in construction supply chain management: a systematic review, International Journal of Construction Management, Vol. 20, n.° 5, pp. 490-509, DOI: 10.1080/15623599.2018.1488089
McKinsey Global Institute. (2017). Reinventing Construction: A Route to Higher Productivity. Research Insight Impact. E-book versions of selected MGI reports are available at MGI’s website: www.mckinsey.com/mgi
P. Sivaraman, T. Nithyanandhan, S. Lakshminarasimhan et al., (2020). Productivity enhancement in engine assembly using lean tools and techniques, Materials Today: Proceedings, DOI: https://doi.org/10.1016/j.matpr.2020.04.010
Pasquire, C. (2012). Positioning Lean within an exploration of engineering construction, Construction Management and Economics, Vol. 30, n.° 8, pp. 673-685. DOI: 10.1080/01446193.2012.689431
Pérez, G. J., Del Toro, H. Y., y López, A. M. (2019). Mejora en la construcción por medio de lean construction y building information modeling: caso estudio. RITI Journal, Vol. 7, n.° 14, pp. 111-118.
Produktiva. (2018). Manual del Sistema de Producción de Produktiva. Basado en Last Planner System. Vol. 1, n.° 1
Rojas, M. D., Henao, M., y Valencia, M. E. (2016). Lean construction – LC bajo pensamiento Lean. Revista Ingenierías Universidad de Medellín, Vol. 16, n.° 30, pp. 115-128.
Salem, O., Solomon, J., Genaidy, A., Luegring, M. (2005). Site implementation and assessment of LC techniques. Lean Constr J. Vol. 2, n.° 2, pp. 1–21.
Sinesilassie, E.G., Tabish, S.Z.S., Jha, K.N. (2017). Critical factors affecting schedule performance: A case of Ethiopian public construction projects–engineers’ perspective. Eng Constr Arch Man. Vol. 24, n.° 5, pp. 757–773.
Tsao, C.C., Draper, J. & Howell, G.A. (2014). An Overview, Analysis, and Facilitation Tips for Simulations That Support and Simulate Pull Planning. 22nd Annual Conference of the IGLC. Oslo, Norway.